August 2016 - July 2021:
Wheelabrator Kemsley K3 CHP
WHEELABRATOR Kemsley K3 CHP
Sittingbourne, Kent United Kingdom
75mw Gross, 1680 tonne/day Energy-from-waste power plant
Serving as Commissioning Manager for new-build energy-from-waste (EfW) power plant in the United Kingdom. Responsible for wide range of activities including:
design review, operability and maintainability focus
construction management support
works acceptance / handover to commissioning
client representative at key factory acceptance tests
QA/QC review
coordination of all commissioning and training activities between Wheelabrator O&M Staff and EPC contractor
lead interface with CHP steam off-taker and landlord, DS Smith
lead interface with Environment Agency for all commissioning activities
Selected from within Wheelabrator organization to move from the US to the UK to support the Kemsley project. Expatriate assignment at high cost to the organization, responsible for delivering a new facility that is consistent with US best practices:
integration of US facilities O&M systems and standard operating procedures
key involvement in O&M staff hiring and mobilization
implementation of lessons learned from operational facilities in the UK and US
coordination and ongoing knowledge sharing with colleagues on other active UK construction projects
leading by example the Wheelabrator Vision and Values
What makes this project unique?
SIze and Scale
Largest facility built by CNIM in UK as EPC contractor
Over £330M capital investment
Highest thermal efficiency EfW facility in the UK
Most profitable facility in Wheelabrator fleet (US or UK)
Overcoming Challanges
Subcontractor insolvency and commercial issues
Constructibility issues due to vertical boiler design
First project-financed and first merchant EfW project in UK
International project / management of multiple cultures
Commissioning facility during COVID-19 Pandemic
Leaving a Legacy
Responsible for a large number plant design improvements that will reduce O&M expense for the next 40 years, the term of the site Lease and Steam Supply Agreement with DS Smith
Implementation of new ideas and technologies to drive continuous improvement
Assembled superior O&M team in a very competitive labor market
Project Gallery:

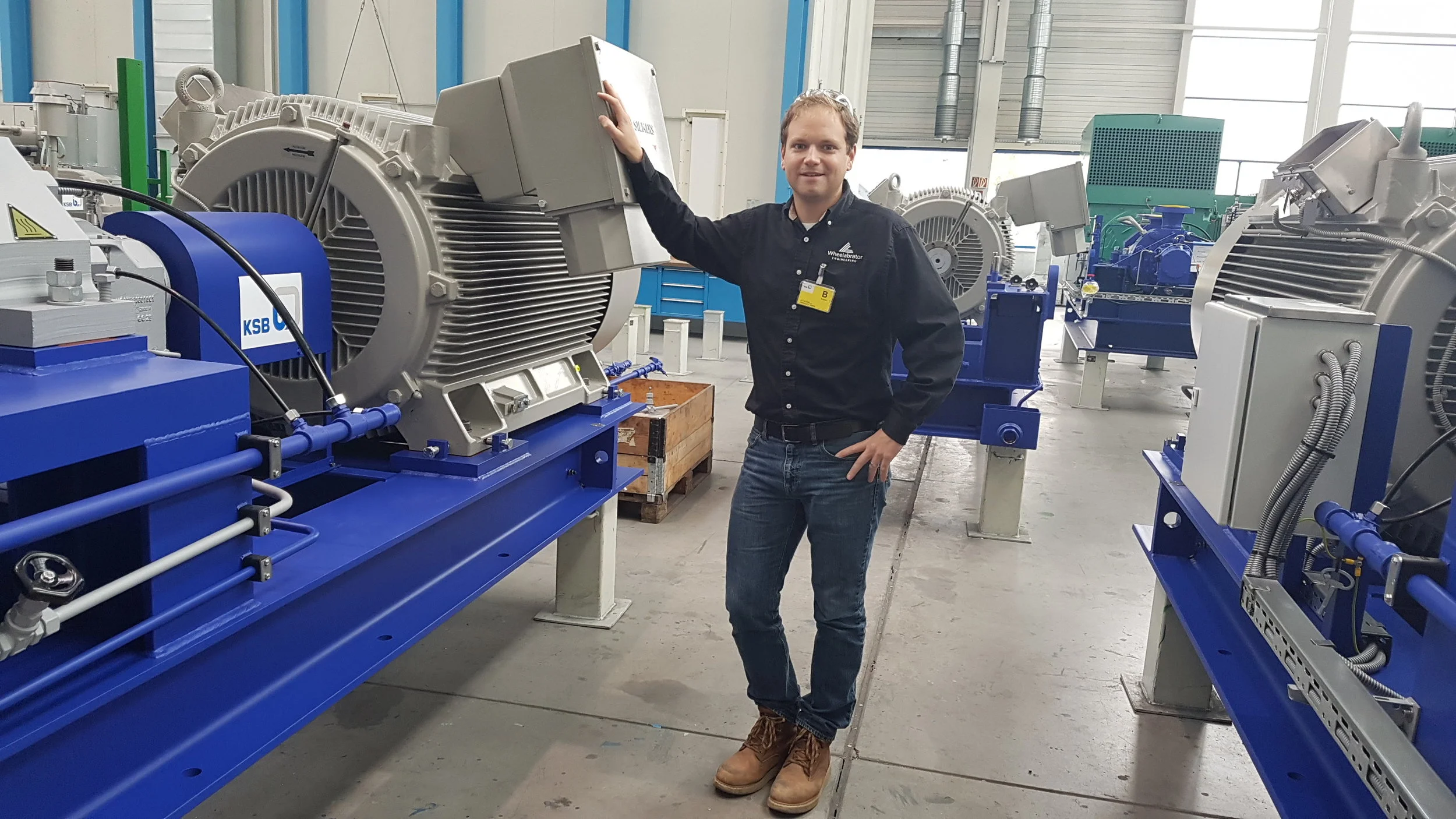
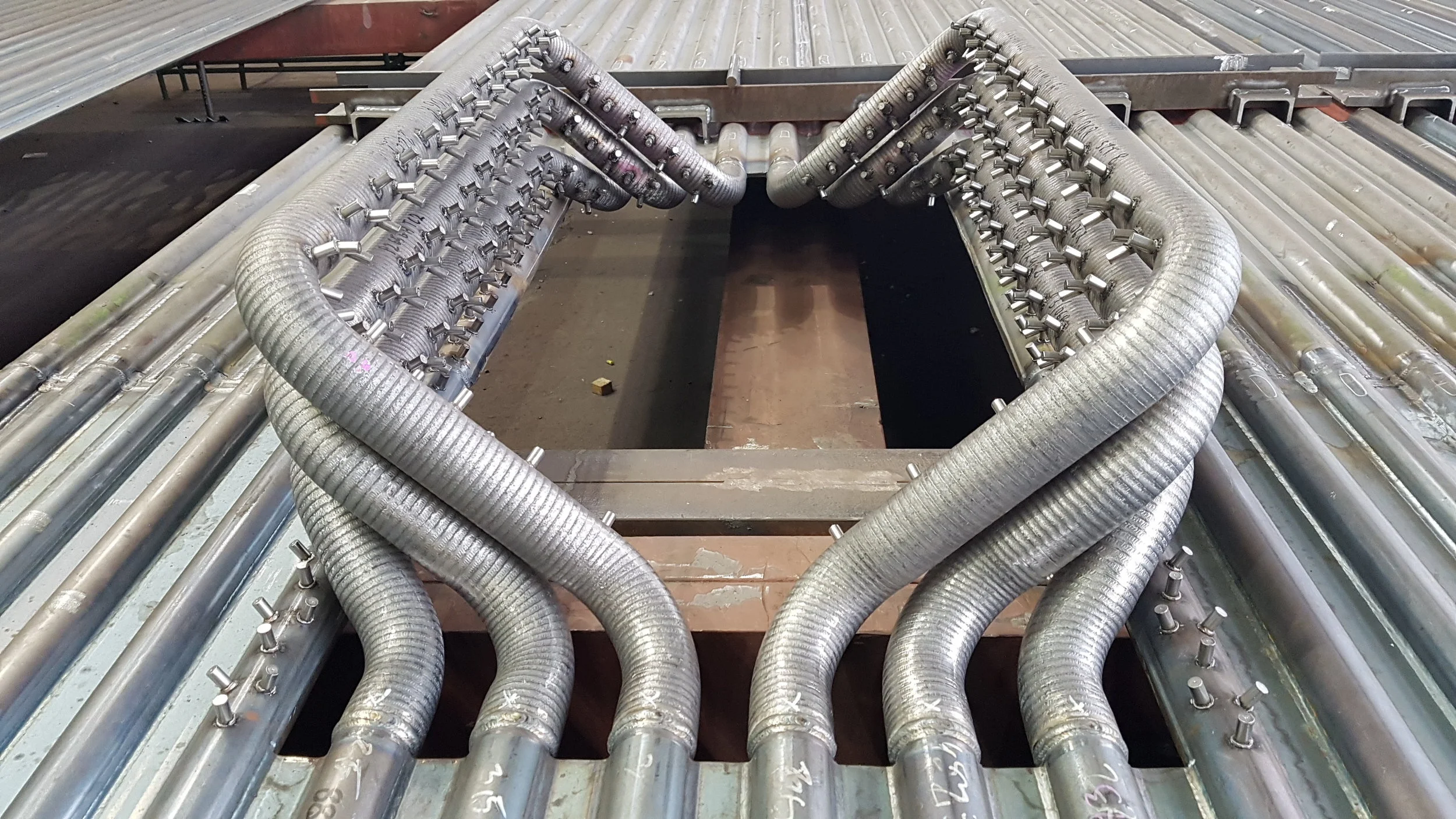
April 2016 - July 2016
Wheelabrator Shasta Turbine Generator Casualty
Wheelabrator shasta Energy
anderson, califronia, usa
55mw gross, 1250 ton/day woody biomass fired power plant
On April 28th, 2016 Wheelabrator experienced the worst turbine generator casualty in the company’s history at the Shasta biomass facility. A failure of the plant 110VDC battery charger went unnoticed during a plant upset the previous week. As the DC voltage ran down, an unknown legacy design issue resulted in the three turbine generators tripping on low DC voltage without being able to open the generator circuit breakers. The operations team opened an off-site utility circuit breaker to stop the generators motoring, but no DC power remained to run the emergency lube oil pumps. All three turbine generator sets crashed down without lube oil resulting in significant damage.
I was called into our SVP of Operations office at 0900 and informed that I had been selected to manage the investigation and subsequent repairs. I was on a plane at 1700 heading to California.
This was not a typical outage which made the required repairs even more challenging. The added pressure of dealing with the insurance company and their technical consultants made this a truly unique experience. We completed three simultaneous overhauls/inspections with all three turbine rotors and all three generator rotors leaving the site for journal machining repairs. Considering this expansive scope, and the fact that we had never done an overhaul on more than one of these machines at the same time, the following total outage times are remarkable:
June 06, 2016 - All three units disassembled simultaneously for the first time in the 29 year history of the plant
July 10, 2016 - Unit 2 was the last unit returned to service 74 days after the initial incident
August 2015-January 2016
Wheelabrator Corporate Office Relocation
Wheelabrator Technologies HQ
Hampton, NH to Portsmouth, NH USA
Shortly after the sale of the Wheelabrator business from Waste Management, Inc. to Energy Capital Partners, the new Senior Leadership Team decided to sell the office at 4 Liberty Lane in Hampton, NH and build out a new leased office space in Pease Tradeport, Portsmouth, NH. I was selected to manage the entire project, reporting directly to the new CEO on a very fast-track implementation of this office move.
This was my first experience in commercial construction, but a great experience to leverage previous skills on industrial and power work. The ability to execute this project on time and within budget demonstrates my versatility and willingness to take on new challenges. Completed the entire project in a very short timeline; started design in September 2015 and employees started work on January 4th, 2016 in the new office space.
Directly responsible for:
Managing design and permitting process for new office space
Buildout of the new space including contractor selection, budget and schedule management, interface with lessor, procurement of all goods and services
Assisted in new lease negotiation, purchase and sale agreement for the old building
Relocation of employees, corporate server room, performance center, and corporate medical database in one weekend to minimize business interruption across fleet
Worked with colleagues and contractors throughout our fleet of power plants to incorporate informational displays about our Energy from Waste plants
Construction commenced in October 2015
Move in day January 4, 2016
Project Gallery:


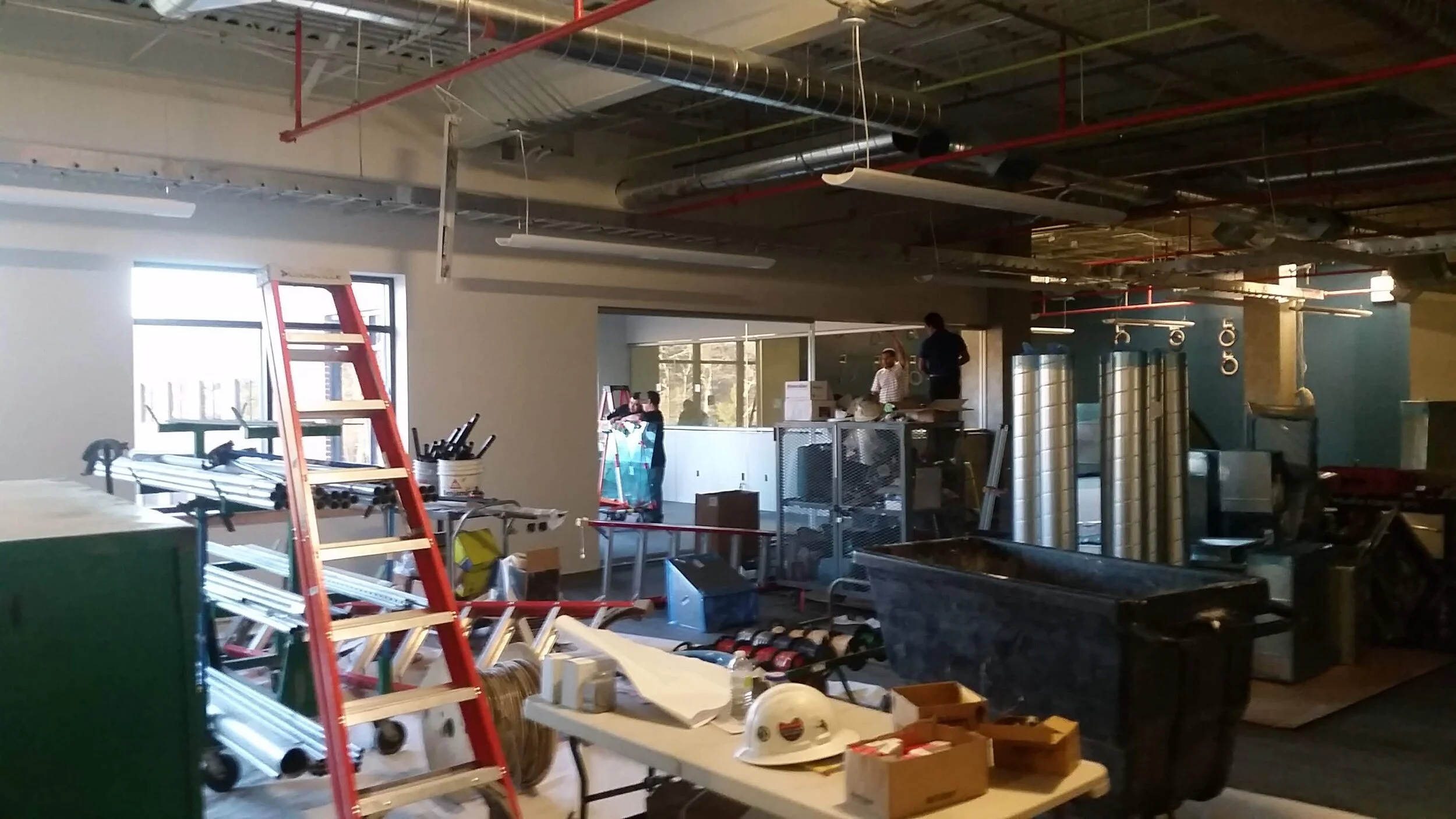

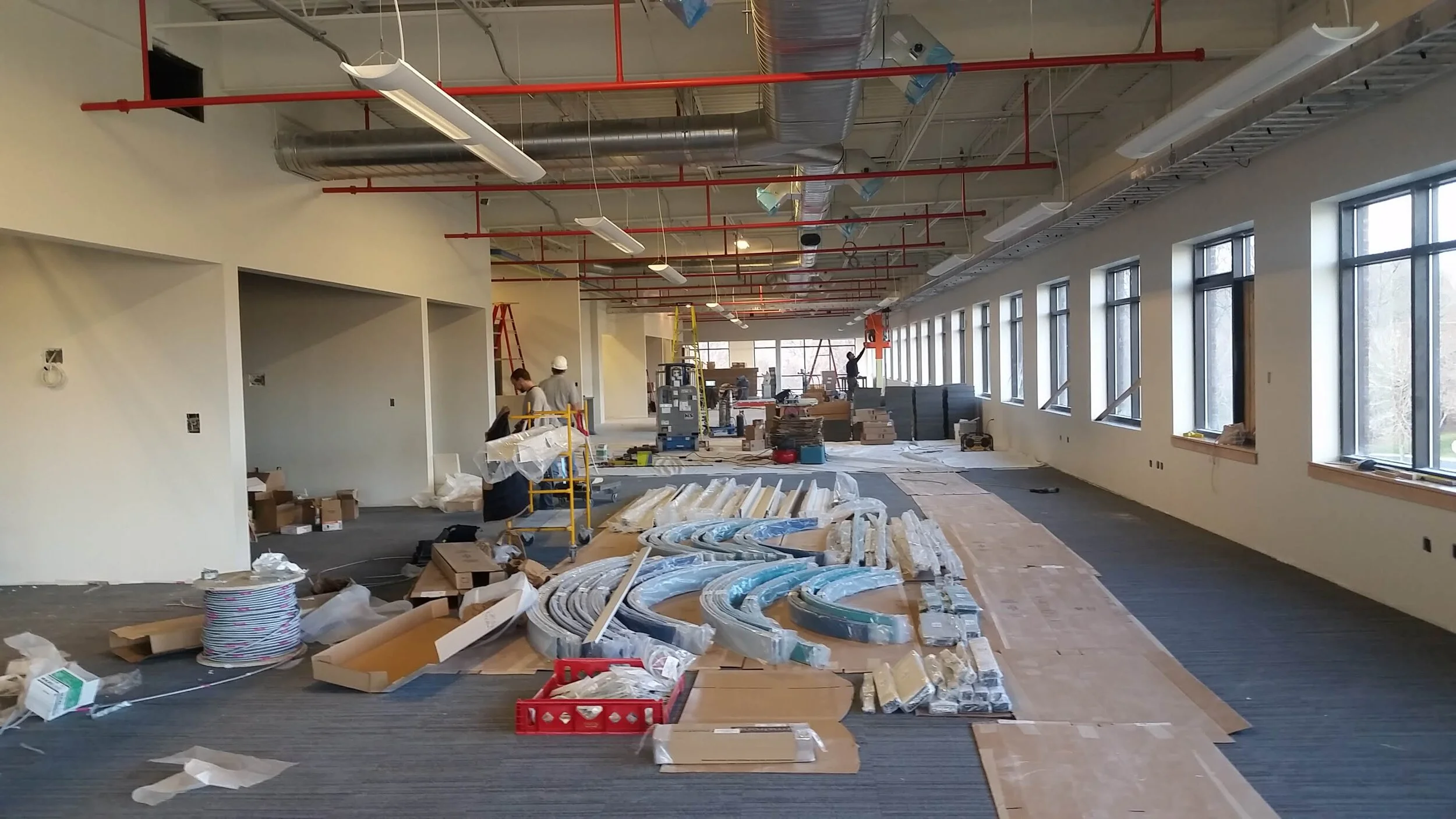
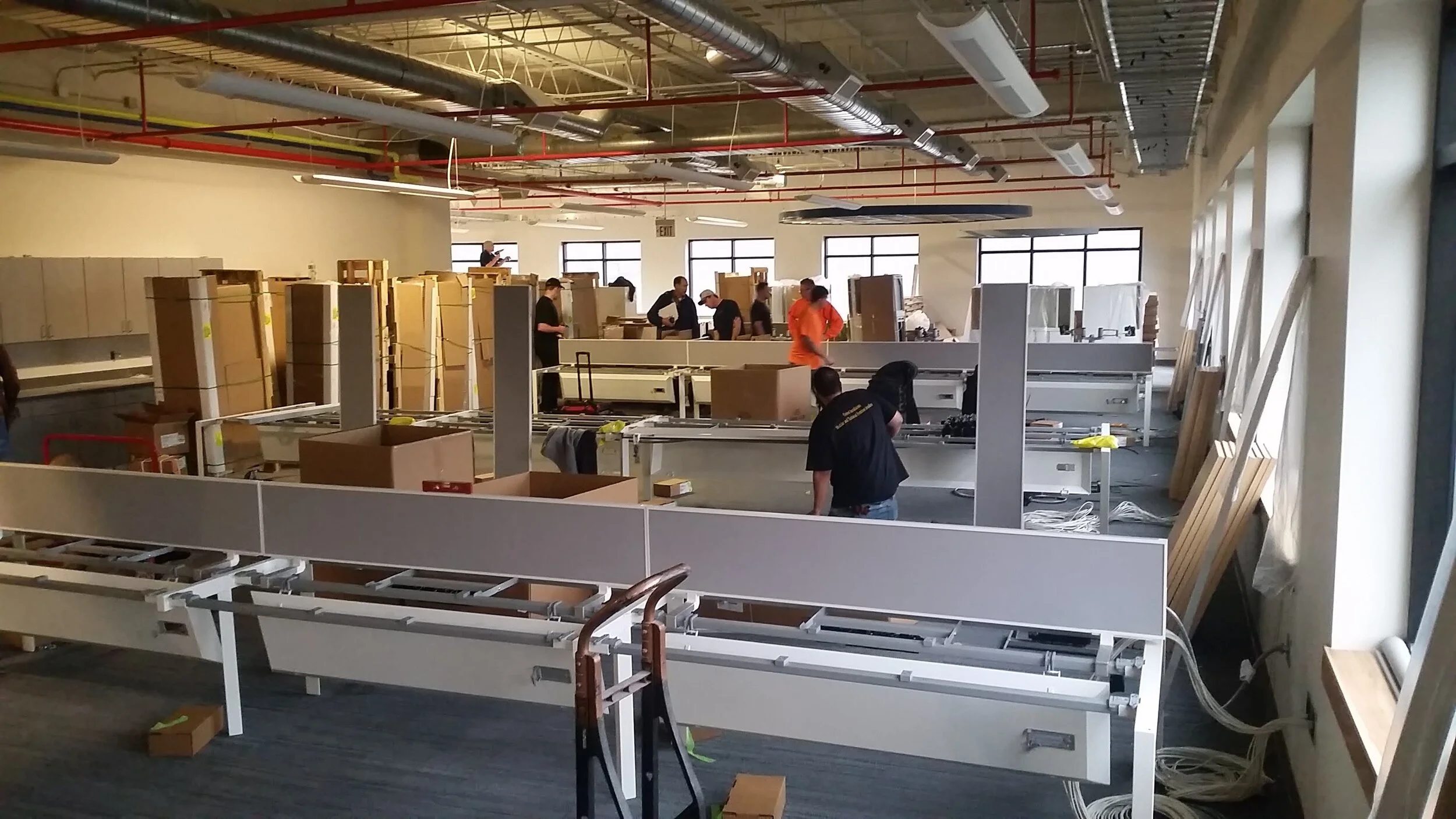
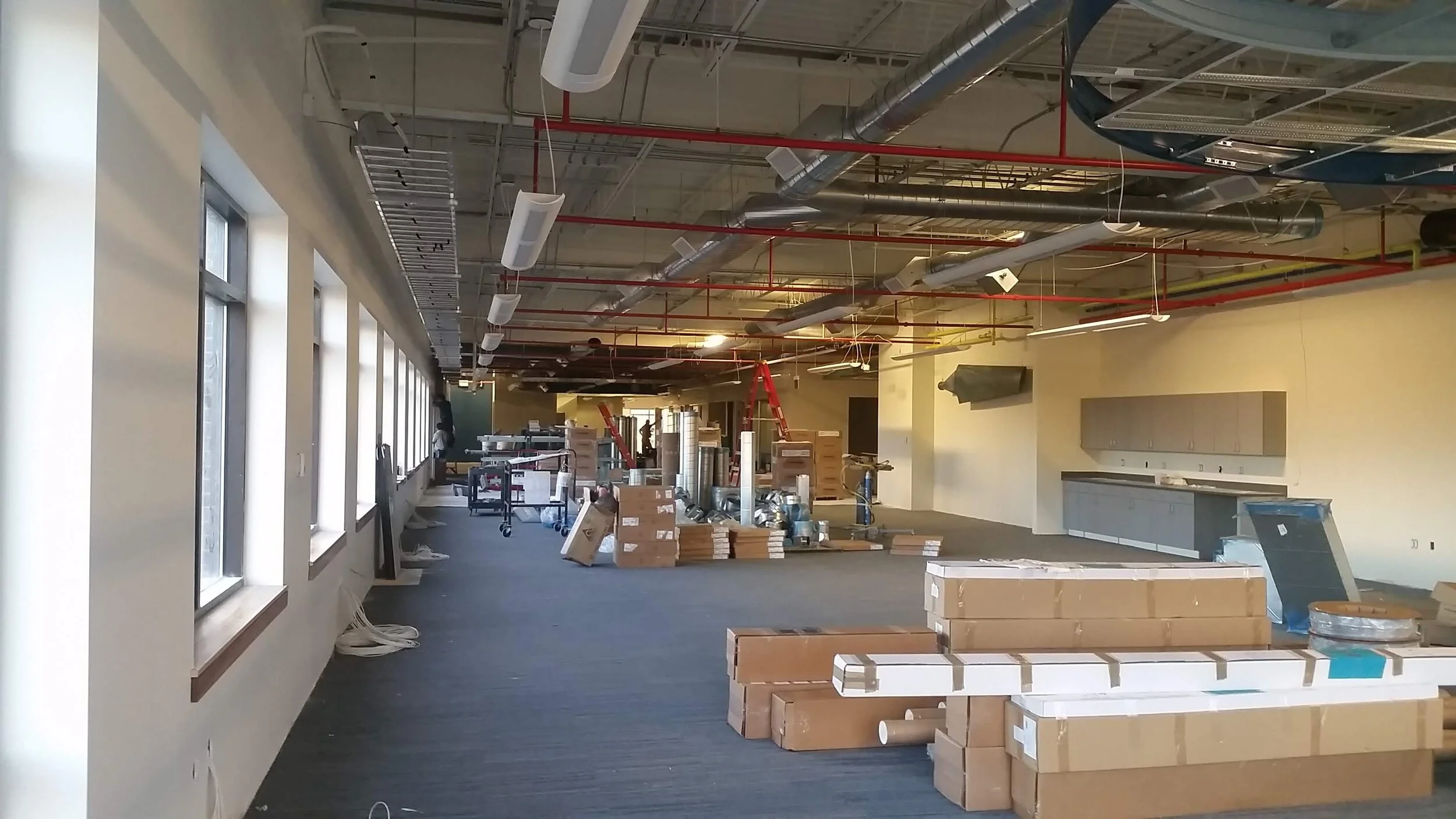
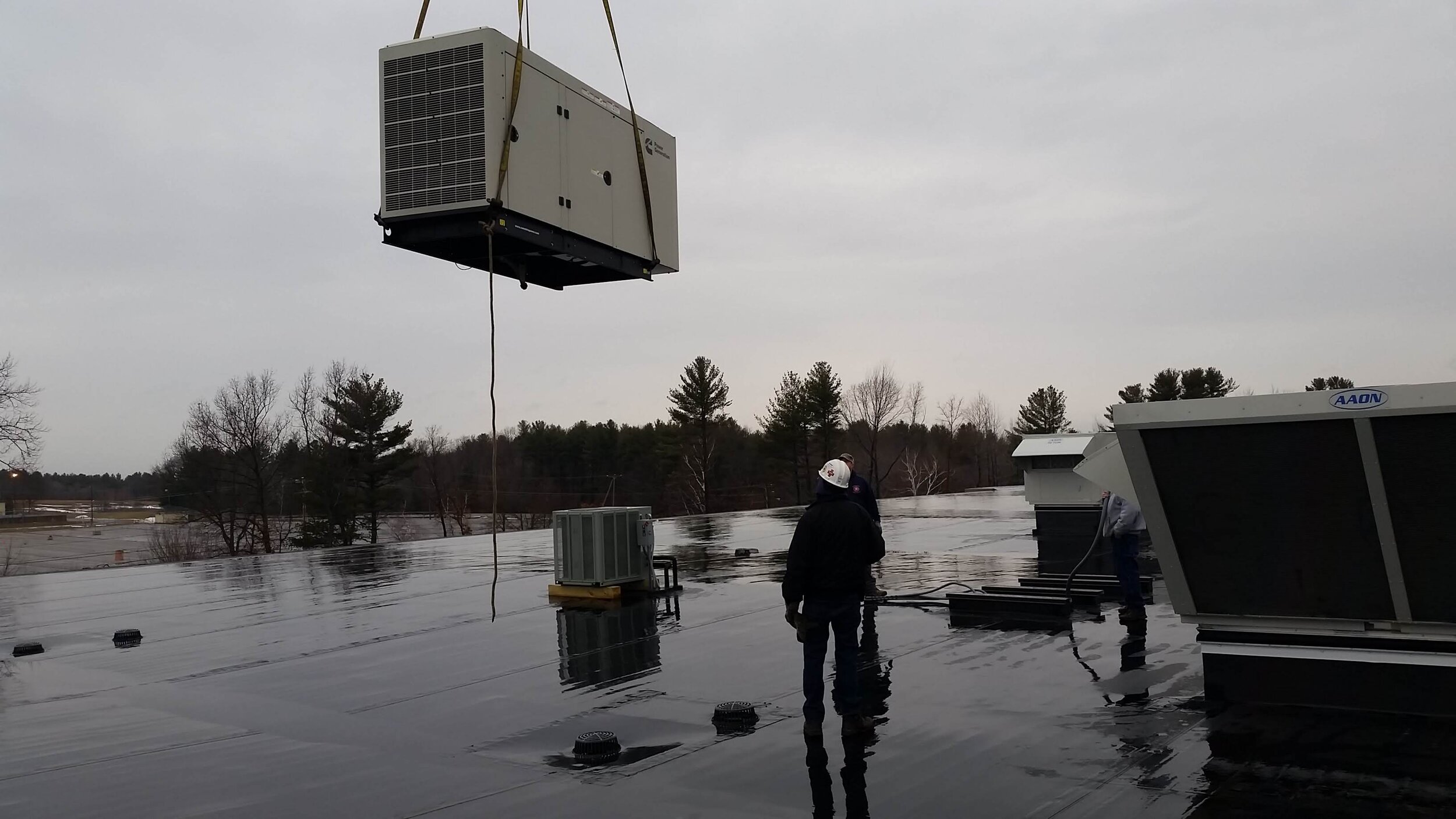
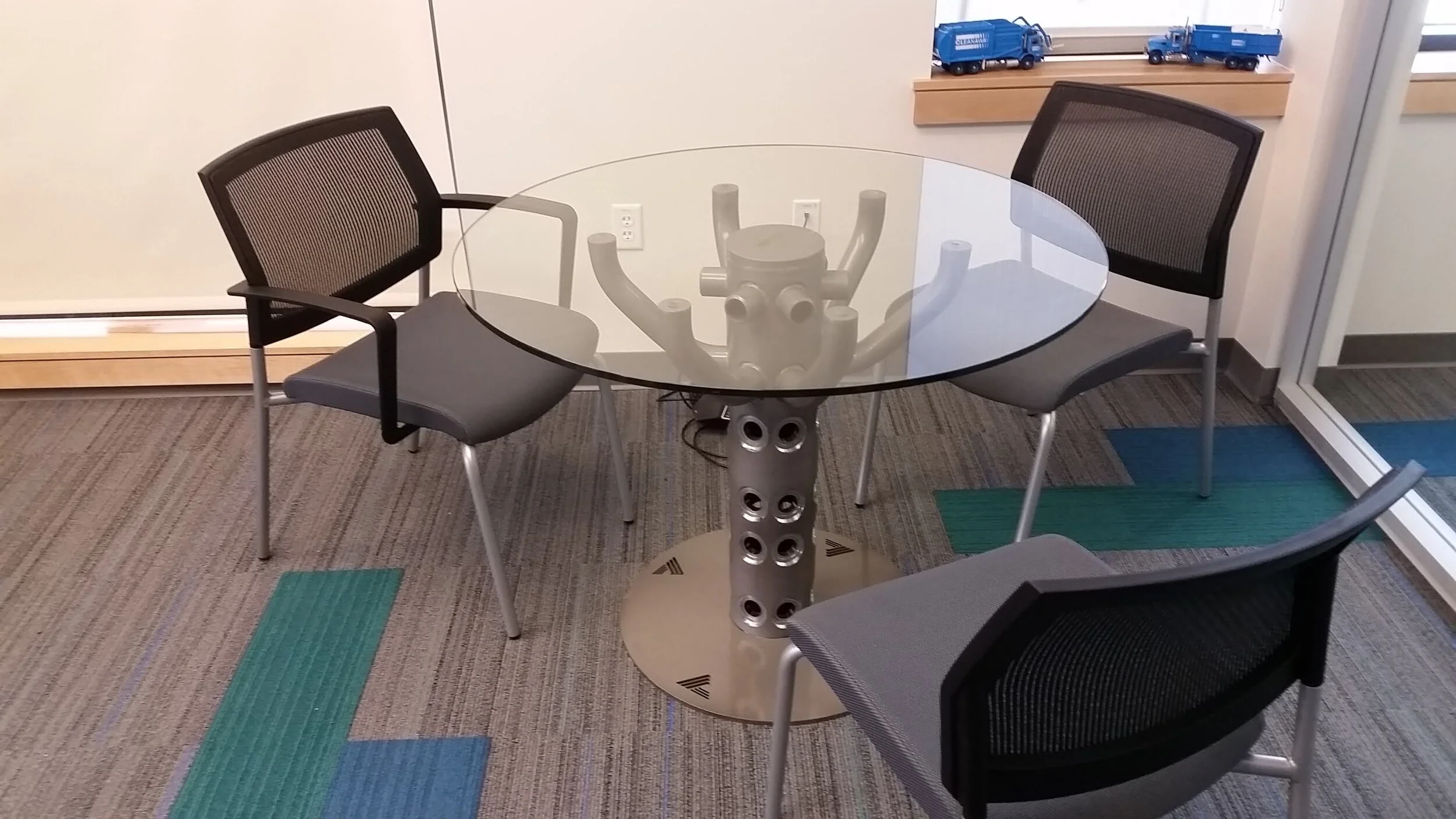

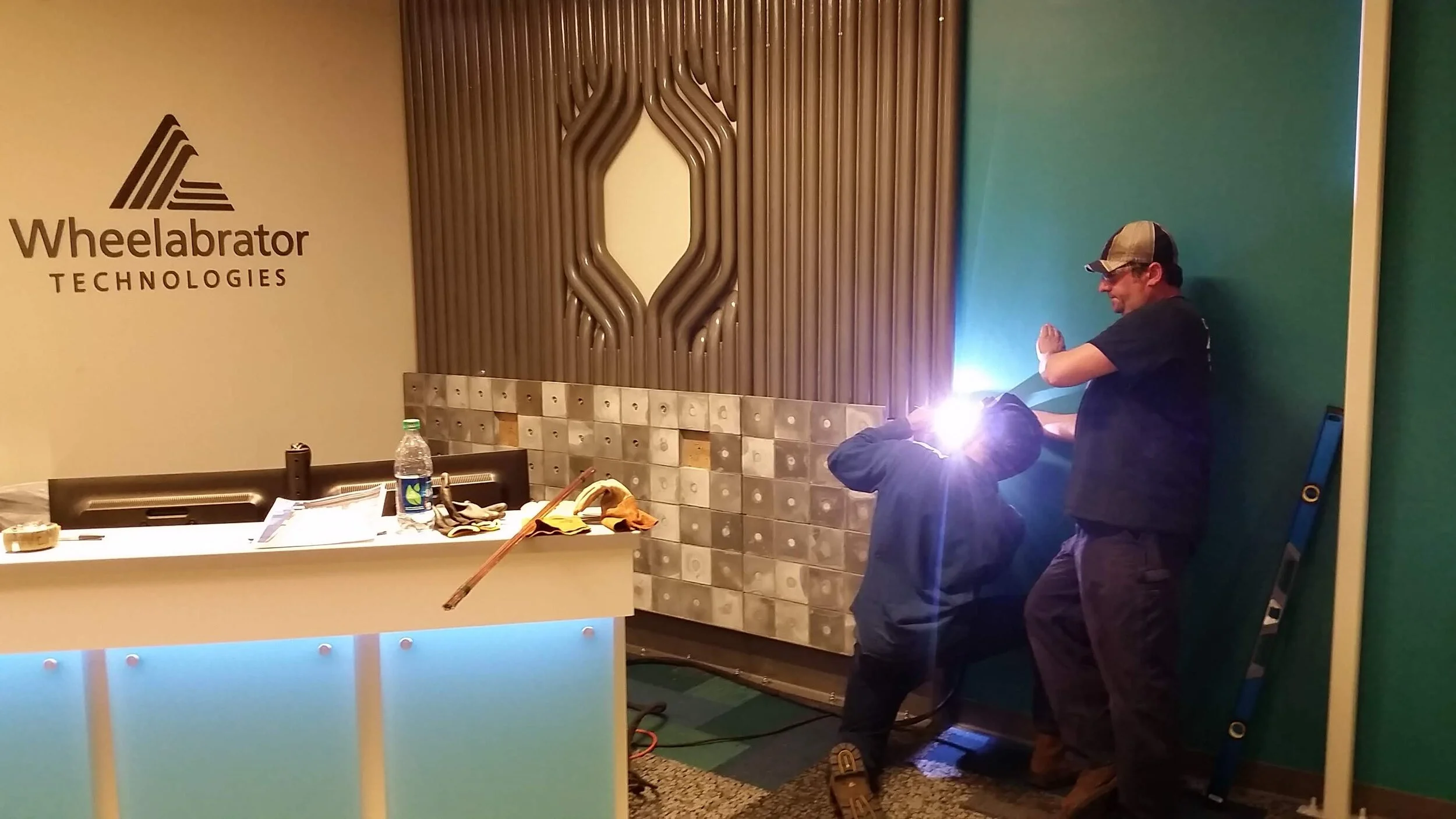
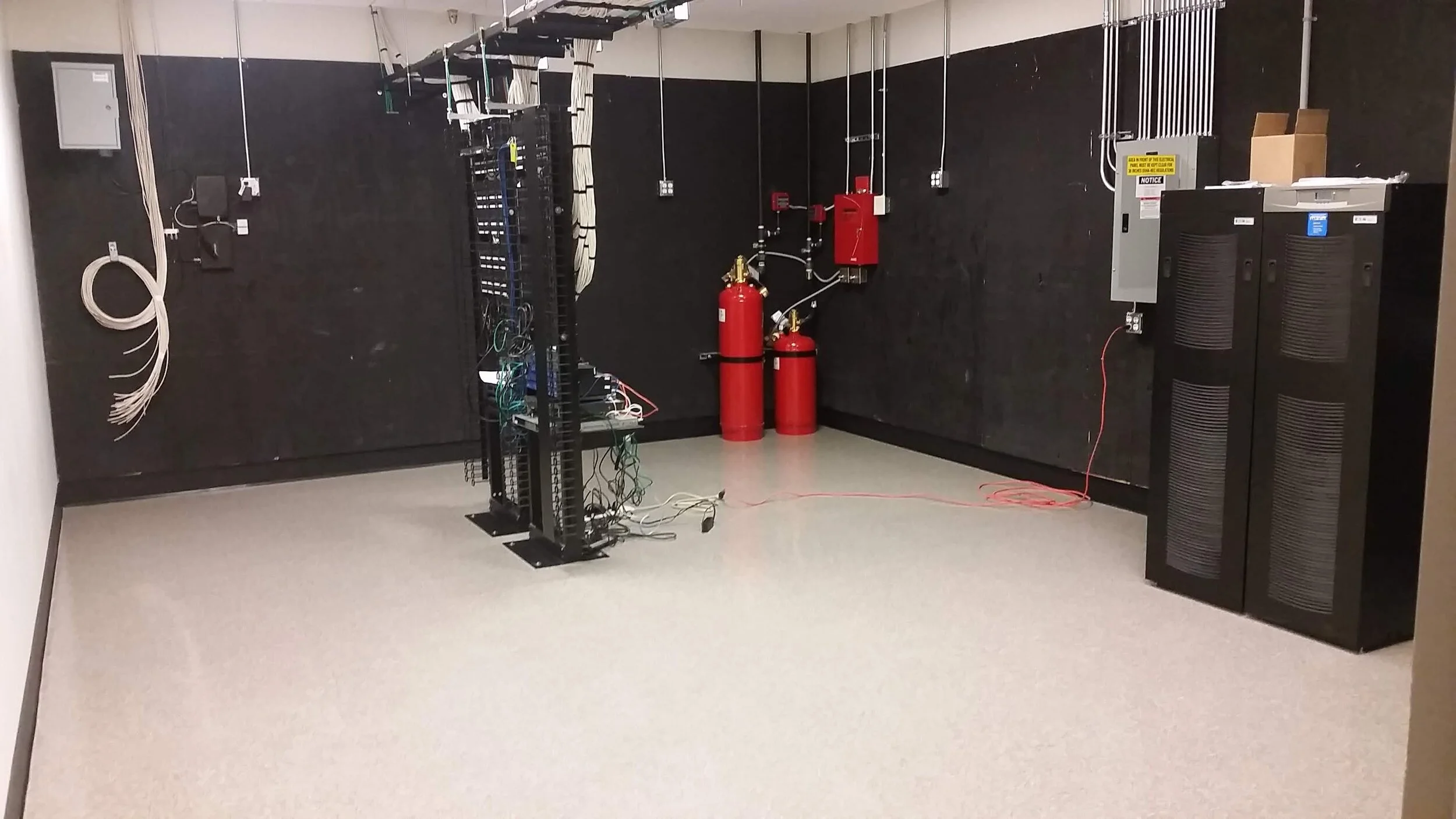
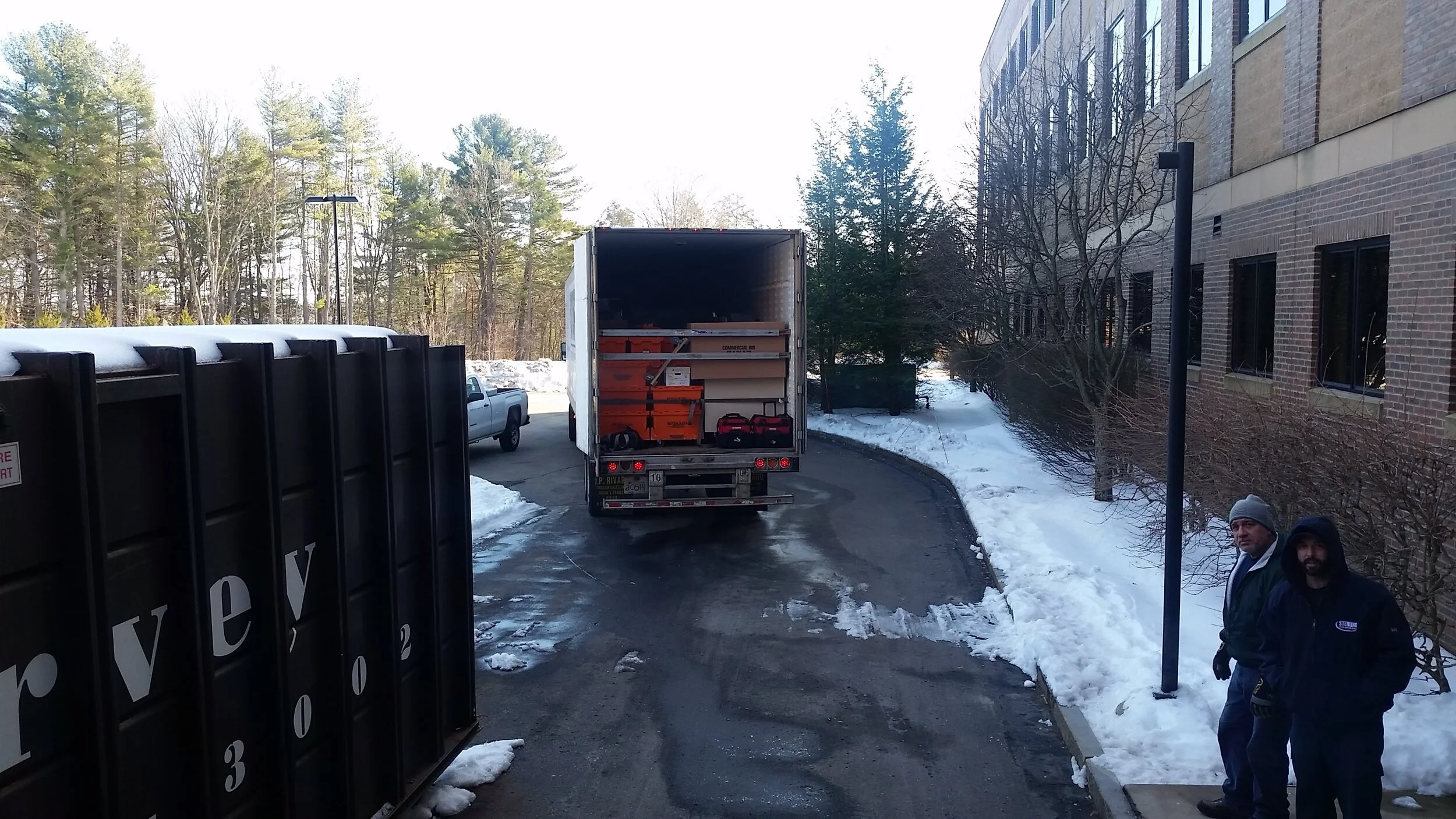

May 2011 - December 2016
Misc. Capital Engineering and Construction Projects
Specializing in project execution of small capital projects at Wheelabrator’s fleet of power plants. Developed a method of planning and execution that proved successful in delivering projects on-time and on-budget while minimizing impact to facility operations and availability.
Bridgeport metals recovery / ash handling system modifications
Wheelabrator Bridgeport - Bridgeport, CT - 67 MW, 2,250 TPD Energy-FROM-WASTE Power Plant
Total Project Cost: $1,200,000 – 21.5% IRR, improved non-ferrous recovery revenues
• Project Engineer/Project Manager for the modification of an existing metals recovery and ash processing system at the WTI Bridgeport Facility
• Developed strategy to minimize system downtime during construction. 9 day system outage
• Project successful; on-time and on-budget
Westchester Export steam line / chp conversion
WHEELABRATOR Westchester - Peekskill, NY - 60 MW, 2,250 TPD Energy-FROM-WASTE Power Plant
Total Project Cost: $2,900,000 – 23.5% IRR, new steam sales revenues
• Project Engineer/Project Manager for the installation of an entirely new export steam line from the WTI Westchester Facility to a neighboring industrial laundry facility
• Managed the procurement process for the selection of a design-build (EPC) contractor
• Managed system start-up team and turn-over to the facility
• Project successful; on-time and on-budget
Concord metals recovery / ash handling system modifications
Wheelabrator Concord - Penacook, NH - 14 MW, 500 TPD Energy-from-waste Power Plant
Total Project Cost: $4,300,000 – 15.5% IRR, new ferrous and non-ferrous scrap metal sales revenues
• Project Engineer/Project Manager for the installation of an entirely new metals recovery and ash processing system at the WTI Concord Facility
• Developed strategy to minimize system downtime during construction
• Worked with plant personnel, consulting engineers, and equipment suppliers to design the system in the most cost effective and practical layout
• Project successful; on-time and on-budget